Greatest Guide to Metal Stamping Techniques and Applications
Wiki Article
Releasing the Potential of Metal Stamping: Specialist Tips and Ideal Practices Revealed
In the world of steel stamping, where accuracy and performance regime supreme, the quest to maximize processes and unlock hidden potentials is a continuous search. As we navigate via the intricate globe of metal stamping, a closer look at the details of tooling layout, material option, production effectiveness, high quality control, and arising fads assures a prize chest of insights waiting to be uncovered.Tooling Layout Optimization
Optimizing tooling design is vital for enhancing performance and precision in metal stamping procedures. A well-balanced tooling layout can considerably influence the high quality and cost-effectiveness of metal stamping procedures. By thoroughly considering elements such as product choice, die configuration, and part geometry, suppliers can simplify manufacturing processes and improve total item quality.One key aspect of tooling design optimization is selecting one of the most suitable materials for the punches and dies made use of in the stamping procedure. Materials with high wear resistance and strength are preferred to ensure long life and decrease tooling upkeep demands. Furthermore, pass away setup plays an essential duty in achieving harmony and consistency in stamped parts. Appropriate die style can aid stop problems such as wrinkling, tearing, and too much springback, causing greater production yields and lowered scrap prices.
Moreover, maximizing part geometry through tooling design can aid minimize product waste and production time. By carefully shaping punches and dies to match the preferred component requirements, manufacturers can attain tighter tolerances and improved part high quality. Generally, investing time and resources in optimizing tooling layout can cause substantial lasting advantages for metal stamping procedures.

Product Option Methods
Tactically picking materials for metal marking tooling is vital for guaranteeing sturdiness and performance in manufacturing procedures. When picking materials for steel stamping applications, numerous vital aspects need to be thought about.Another vital variable in product selection is the anticipated manufacturing quantity - Metal Stamping. For high-volume production runs, tooling products with premium wear resistance and sturdiness, such as device steels or carbide, are commonly liked to stand up to the rigors of continual stamping operations
In addition, the intricacy of the stamping style and the needed accuracy likewise play a considerable role in material selection. For detailed stamping patterns or limited tolerances, materials with high thermal conductivity and superb machinability, like beryllium copper or device steel alloys, might be better to accomplish the desired results.
Manufacturing Performance Methods
To boost manufacturing output and decrease production costs, executing effective strategies in metal stamping processes is vital. Automated steel stamping devices can execute jobs with precision, consistency, and at a much faster rate than hand-operated labor, leading to enhanced efficiency and decreased cycle times.
An additional method to enhance manufacturing efficiency is with continual procedure improvement. Conducting normal audits and performance assessments can help recognize traffic jams, inefficiencies, and areas for enhancement within the metal stamping procedure. By evaluating data and comments from these examinations, manufacturers can execute targeted services to simplify procedures, boost throughput, and make the most of overall efficiency.
Furthermore, taking on lean manufacturing concepts, such as five method and Kanban systems, can assist remove waste, improve workflow, and boost overall productivity in metal stamping operations. By promoting a culture of continual enhancement and empowering employees to add concepts for efficiency gains, makers can unlock the full this content possibility of their steel marking procedures.
Top Quality Control Procedures
Structure on the structure of effective manufacturing strategies in metal marking processes, guaranteeing rigid quality assurance steps is important for maintaining product requirements and consumer complete satisfaction. Quality control in metal marking involves organized examination, screening, and surveillance of the manufacturing processes to identify and fix any type of deviations or defects that can jeopardize the end product's honesty (Metal Stamping). Applying procedures such as regular equipment maintenance, in-process assessments, and detailed screening of finished components can aid spot concerns at an early stage and protect against pricey rework or product remembersRoutine audits and reviews of high quality procedures can help identify locations for improvement why not try this out and ensure consistency in item quality. By cultivating a society of top quality awareness amongst workers and offering sufficient training on top quality control procedures, suppliers can boost general product dependability and brand name track record.
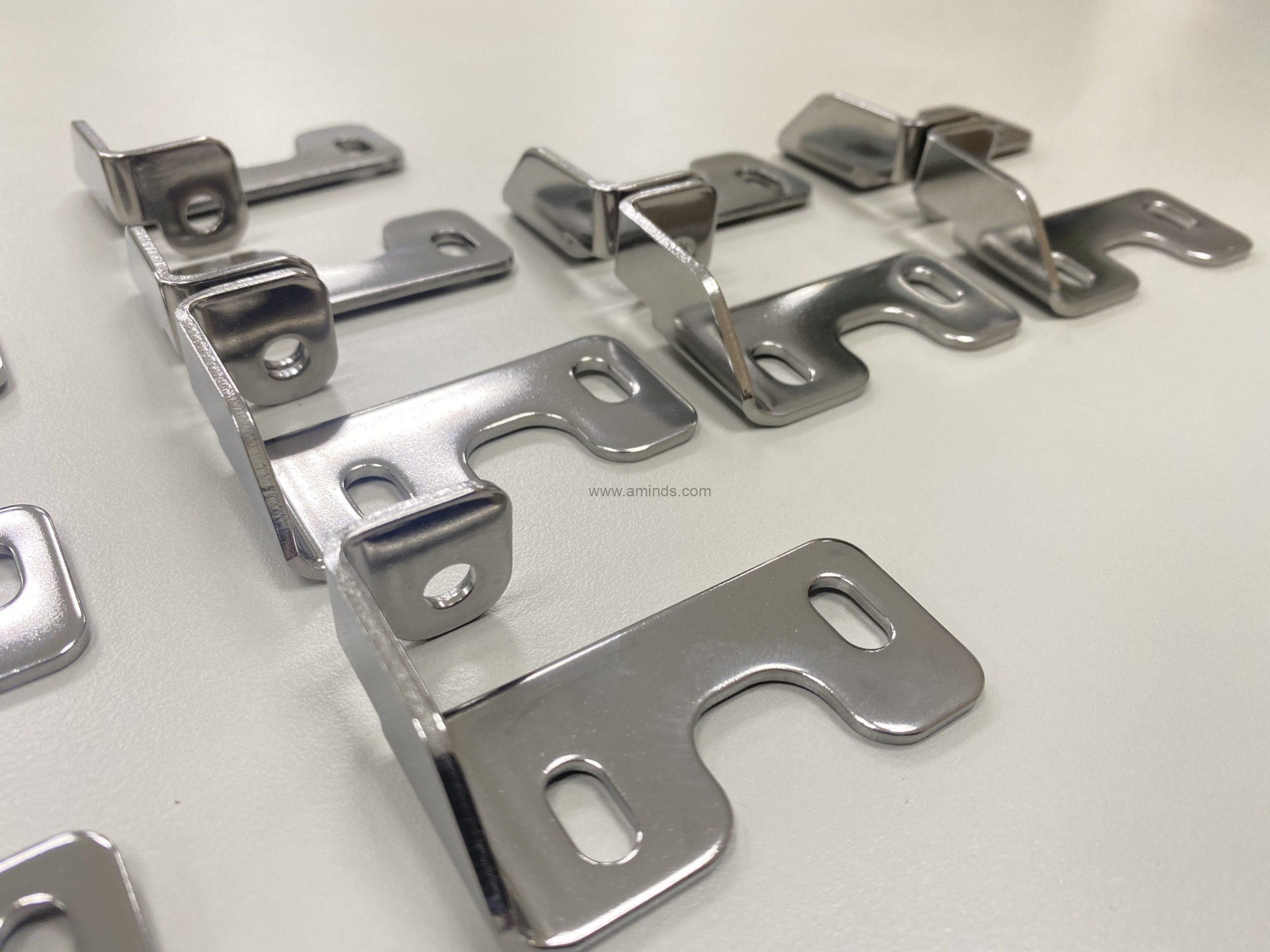
Ingenious Metal Stamping Technologies
Developments in metal marking innovations have actually reinvented the production sector, improving efficiency and precision in the manufacturing process. Servo presses use unrivaled control over the marking process, enabling for changes in speed, dwell, and force time with extraordinary precision.
Furthermore, the adoption of additive production methods in steel stamping, such as 3D printing of die parts, has streamlined the tooling style and production process. This method enables better style versatility, rapid prototyping, and expense savings in tooling manufacturing. By leveraging these innovative modern technologies, manufacturers can open new levels of performance, high quality, and competitiveness in the metal stamping market.
Final Thought
Finally, the optimization of tooling layout, strategic material choice, reliable production techniques, quality assurance procedures, and ingenious technologies are important for releasing the complete capacity of metal stamping. By executing these ideal techniques and professional pointers, makers can enhance productivity, increase top quality, and remain competitive in the metal stamping market. It is critical for firms to constantly examine and enhance their procedures to accomplish success in this area.As find more we navigate through the elaborate globe of steel marking, a better look at the details of tooling design, material selection, production performance, high quality control, and arising trends assures a treasure trove of insights waiting to be uncovered. A well-thought-out tooling style can dramatically affect the quality and cost-effectiveness of metal stamping operations.Building on the structure of effective manufacturing strategies in steel stamping processes, guaranteeing stringent quality control steps is imperative for maintaining item standards and customer fulfillment. Quality control in steel marking involves systematic inspection, screening, and tracking of the production processes to identify and correct any variances or flaws that might jeopardize the last product's stability.In conclusion, the optimization of tooling layout, strategic material option, effective production strategies, quality control procedures, and ingenious innovations are important for unleashing the full potential of metal stamping.
Report this wiki page